The lathe machine, a fundamental tool in various manufacturing and engineering processes, has been a cornerstone of industrial production for centuries. Despite its widespread use and importance, the lathe machine can pose significant safety risks if not operated or maintained properly. One such incident involving a lathe machine highlights the critical need for strict safety protocols and operator vigilance. On a typical day at a medium-sized manufacturing facility, a seasoned machinist with over a decade of experience was tasked with producing a series of cylindrical parts using a computer numerical control (CNC) lathe machine.
The machinist, well-versed in the operation of such machines, had completed numerous similar tasks without incident. However, on this particular day, a combination of factors would lead to a serious accident. The machinist, in a rush to meet a tight deadline, failed to properly secure the workpiece, a critical step in ensuring safe operation. Additionally, the machine's safety guard, designed to protect the operator from moving parts, had been removed for maintenance but not replaced as it should have been. The lack of proper training on the updated safety features of the CNC lathe machine also contributed to the operator's complacency.
Key Points
- Proper securing of the workpiece is crucial for safe lathe machine operation.
- Safety guards must always be in place when operating machinery.
- Regular maintenance and inspections are vital for identifying potential safety hazards.
- Operators must receive comprehensive training on machine operation and safety features.
- Complacency can lead to serious accidents, even among experienced operators.
Understanding the Incident
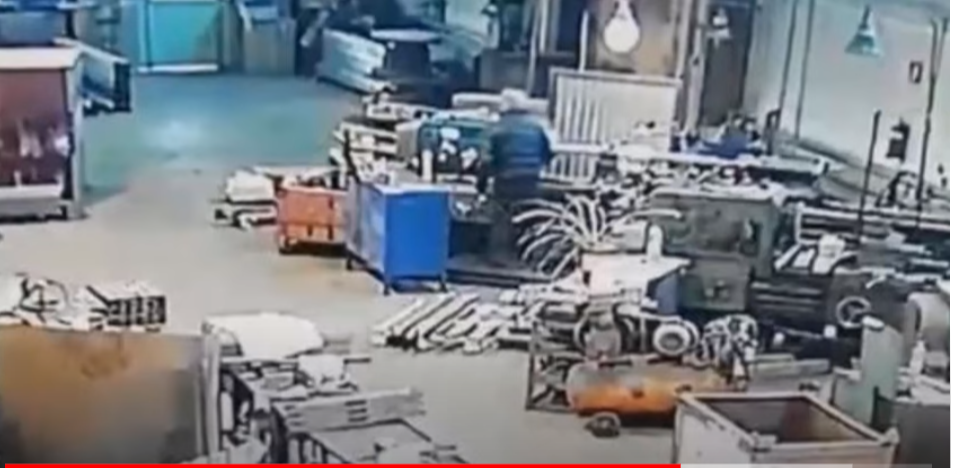
As the machinist initiated the machining process, the improperly secured workpiece became dislodged due to the centrifugal force generated by the high-speed rotation of the lathe. The workpiece, now a dangerous projectile, was ejected from the machine at a significant velocity. The absence of the safety guard meant that there was no barrier to prevent the workpiece from striking the operator. Fortunately, the machinist’s quick reflexes allowed him to partially avoid the impact, but not before suffering serious injuries to his arm and chest.
Investigation and Analysis
An investigation into the incident revealed a multifaceted failure in safety protocols and procedures. The removal of the safety guard without immediate replacement was a critical error, compounded by the operator’s failure to properly secure the workpiece. Furthermore, the investigation highlighted a lack of regular safety inspections and inadequate training programs for operators on new machinery and safety features. The incident served as a stark reminder of the importance of adhering to safety standards and the potential consequences of complacency in a manufacturing environment.
Category | Data |
---|---|
Operator Experience | 10+ years |
Type of Machine | CNC Lathe Machine |
Nature of Injury | Severe lacerations and blunt force trauma |
Root Causes | Improper workpiece securing, absence of safety guard, inadequate training |

Prevention and Safety Measures
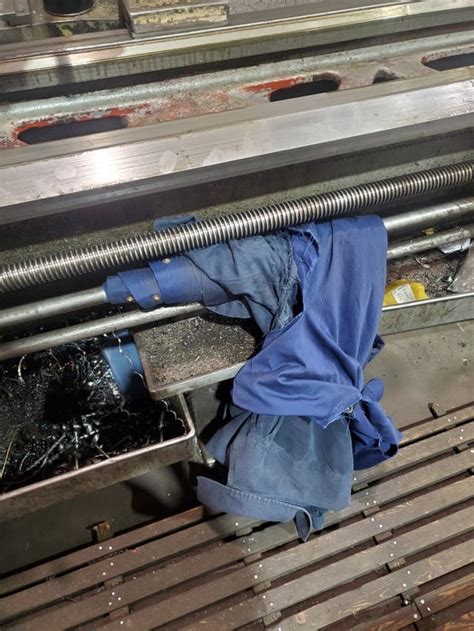
The prevention of such incidents hinges on a multi-faceted approach that includes rigorous training programs, regular safety inspections, and a culture of safety within the organization. Operators must be educated on the proper use of machinery, including the importance of safety guards and the correct procedures for securing workpieces. Furthermore, manufacturers should invest in safety technologies and equipment designed to minimize the risk of accidents, such as automated safety guards and emergency stop systems.
Implementing Safety Protocols
Implementing and enforcing strict safety protocols is paramount. This includes conducting regular inspections of machinery to ensure that safety features are intact and functioning as intended. A culture of safety encourages operators to report any concerns or observations related to machinery operation and safety without fear of reprisal. Additionally, incentives for safe practices and recognition of safe work habits can foster an environment where safety is everyone’s priority.
In conclusion, the lathe machine incident underscores the critical importance of safety in manufacturing environments. Through a combination of proper training, adherence to safety protocols, and a proactive approach to risk management, the likelihood of such incidents can be significantly reduced. As industries evolve and new technologies emerge, the commitment to safety must remain unwavering, ensuring that workplaces are both productive and safe for all employees.
What are the primary causes of lathe machine accidents?
+The primary causes include improper securing of the workpiece, absence or failure of safety guards, operator error due to inadequate training, and lack of regular maintenance and safety inspections.
How can lathe machine accidents be prevented?
+Prevention measures include comprehensive operator training, regular safety inspections, ensuring all safety features are in place and functioning, and fostering a workplace culture that prioritizes safety.
What role does training play in preventing accidents?
+Training is crucial as it educates operators on the safe use of machinery, importance of safety protocols, and procedures for securing workpieces. It also updates them on new safety features and technologies.